· 5 min read
What is SCADA | Definition and Meaning
SCADA, or Supervisory Control and Data Acquisition, is a technology essential for industrial automation, allowing real-time monitoring and control across various sectors.
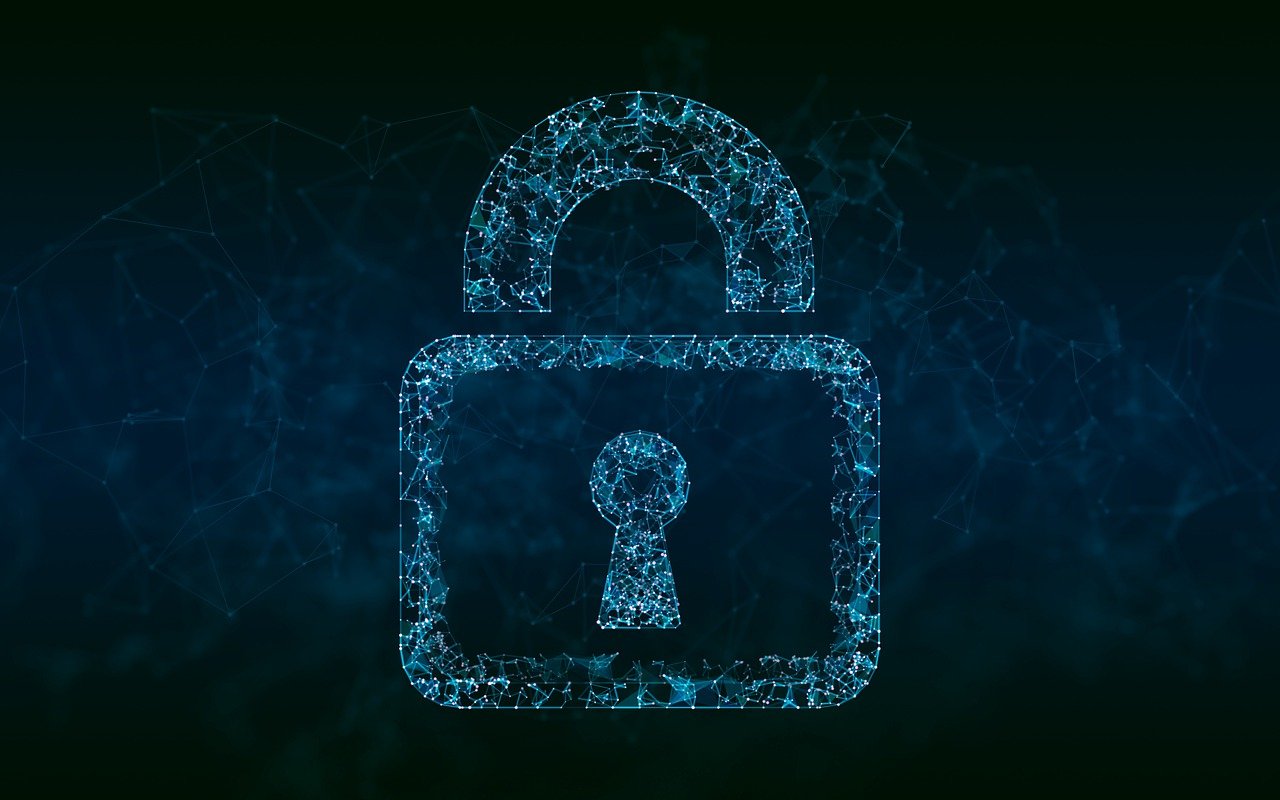
What is SCADA? A Comprehensive Overview
SCADA, which stands for Supervisory Control and Data Acquisition, is an advanced technology that plays a crucial role in industrial automation and control systems. It is a combination of hardware and software that enables operators to monitor and control processes in real-time across various industries. From electric utilities to water treatment plants, SCADA systems are pivotal in enhancing operational efficiency and ensuring safety.
Understanding SCADA
At its core, SCADA is about gathering data from sensors and devices installed in the field and transmitting that data to a central system. This central system allows for the monitoring and control of processes. The key components of SCADA systems include:
- Data Acquisition: This involves collecting real-time data from field devices such as sensors, PLCs (Programmable Logic Controllers), and RTUs (Remote Terminal Units).
- Supervisory Control: Operators could control processes, send commands, and adjust parameters from a central location using a user-friendly interface.
- Communication: SCADA systems used various networking technologies to transmit data between field devices and the control center.
- Data Presentation: The gathered data was presented through graphical user interfaces (GUIs), which made it easier for operators to understand the system�s status.
The Functionality of SCADA
SCADA systems worked by connecting various equipment to a central monitoring unit. The main functionalities included:
Real-time Monitoring: Operators could observe real-time data, which facilitated prompt decision-making. This was particularly vital in scenarios requiring immediate action, such as in power systems or manufacturing plants.
Data Logging: SCADA systems logged historical data, allowing for analysis and reporting. This historical data could be invaluable for performance assessment and predictive maintenance.
Control Functions: Operators could manually control equipment, adjust settings, and implement automatic control strategies.
Alarms and Notifications: SCADA systems were equipped with alarm systems that notified operators of any anomalies or failures in the system.
Data Analysis: Through various analytical tools, SCADA systems helped in analyzing performance trends over time, assisting in optimizing operations and maintenance schedules.
SCADA in Various Applications
SCADA was extensively used across different sectors, including:
- Water and Wastewater Management: Monitoring the integrity of the water supply, treatment processes, and reservoir levels.
- Electric Utilities: Managing the distribution of electricity and monitoring the grid’s stability.
- Manufacturing and Production: Overseeing processes ranging from assembly lines to material handling.
- Oil and Gas: Controlling pipelines, refineries, and distribution systems.
SCADA System Components
A typical SCADA system included several key components:
- Field Devices: Sensors, actuators, and PLCs that collected and managed data.
- Communication Infrastructure: Ensured reliable data transfer, typically consisting of wired or wireless networks.
- SCADA Software: The software component that provided the operator interface, data logging, and system control features.
What is SCADA in Networking?
When discussing SCADA in networking, its role became even more pronounced. SCADA had to communicate over networks, whether they were local or wide-area. This communication enabled real-time data exchange between remote field devices and central control units. Different protocols were used for secure and reliable data transmission.
SCADA Login and Security
Access control was vital for a SCADA system. The SCADA login process ensured that only authorized personnel could manipulate the system. It was essential for maintaining data integrity and system security. Each user was assigned specific permissions according to their role, ensuring a robust security framework.
Known Vulnerabilities
Despite its essential role in industrial systems, SCADA implementations had known vulnerabilities that posed significant risks. Several vulnerabilities were identified in different SCADA products:
Rapid Software LLC’s Rapid SCADA versions prior to 5.8.4 had multiple critical vulnerabilities. These included hard-coded credentials (CVE-2024-21764), an exploit that allowed attackers to redirect users to malicious pages via the login page (CVE-2024-21794), and a zip slip vulnerability allowing attackers to supply malicious configuration files for remote code execution (CVE-2024-21852). Additionally, earlier versions stored plaintext credentials (CVE-2024-21869) and allowed privilege escalation through direct writing to the SCADA directory (CVE-2024-22016).
Schneider Electric’s EcoStruxure Geo SCADA Expert, versions prior to October 2022, suffered from improper output neutralization vulnerabilities (CVE-2023-0595) that could lead to logging misinterpretation when malicious packets were sent. Another vulnerability (CVE-2023-22611) exposed sensitive information to unauthorized actors when specific messages were sent over the database server TCP port.
The Advantech WebAccess system had vulnerabilities that could allow attackers to control servers through maliciously crafted zip files, leading to potential complete control of the SCADA server (CVE-2023-2866).
Spidercontrol SCADA Webserver versions 2.08 and earlier were vulnerable to path traversal attacks, where an attacker with administrative privileges could overwrite important files on the webserver (CVE-2023-3329).
These vulnerabilities highlight the importance of maintaining updated software versions and implementing robust security measures to safeguard against attacks targeting SCADA systems.
Challenges of SCADA Systems
While SCADA offered numerous advantages, it was not without challenges:
- Cybersecurity Risks: SCADA systems often became targets for cyber-attacks. Ensuring strong cybersecurity measures was crucial for protecting against potential breaches.
- Integration Issues: Integrating different types of hardware and software into a cohesive SCADA system could be complicated.
- Dependence on Technology: Over-reliance on automated systems could lead to skill degradation among human operators.
SCADA systems are fundamental in the modern industrial landscape. Their ability to provide real-time data acquisition and control significantly enhances operational efficiency, safety, and reliability. As industries continued to evolve, the importance of SCADA systems will only increase, particularly as new technologies such as the Internet of Things (IoT) reshape the landscape of industrial automation.